
Cement
Cement global significance
Concrete is the second most consumed material globally and cement accounts for 10% to15% by volume of concrete composition. In 2023, the U.S. produced 91 million metric tons of cement, making it the fourth largest global producer.
#2
Most consumed material globally
#4
U.S. global producer ranking
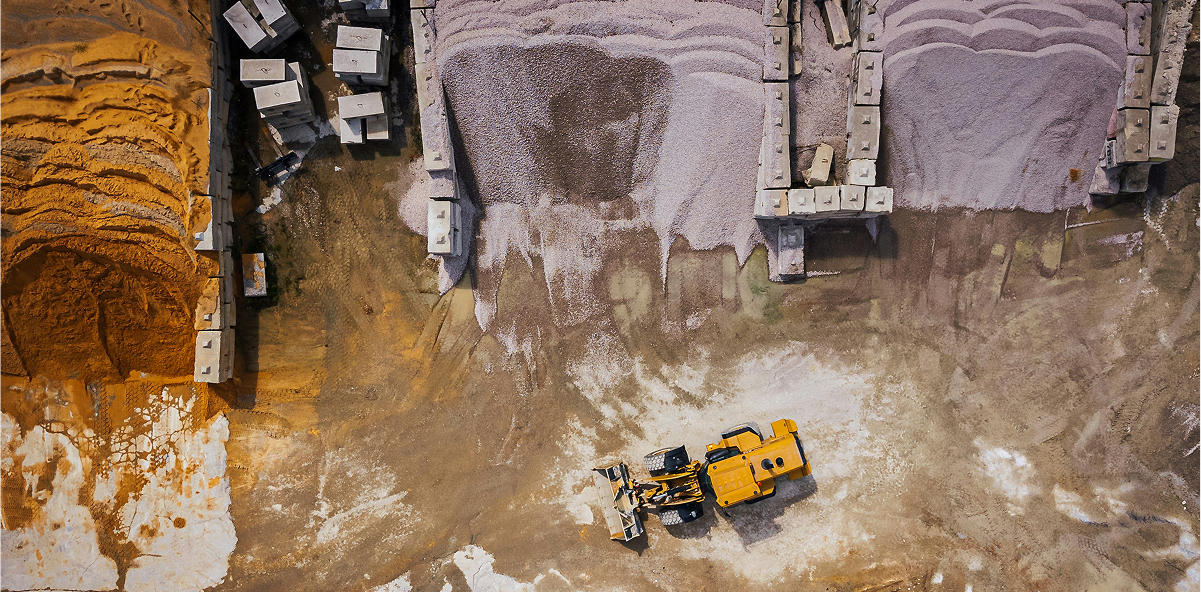
Energy-intensive manufacturing process
The cement manufacturing process involves several unit operations that are significant energy consumers, including quarrying and crushing, preheating, calcination and clinkering in the kiln, and fine grinding.
Pyro processing in the kiln — where the raw materials (limestone, silica and alumina, along with other minor ingredients) are heated to around 1,500°C — is the primary energy-consuming process (accounting for more than 80% of total energy use). Fossil fuels are primarily used for this process, though some fuel switching is practiced in the industry.
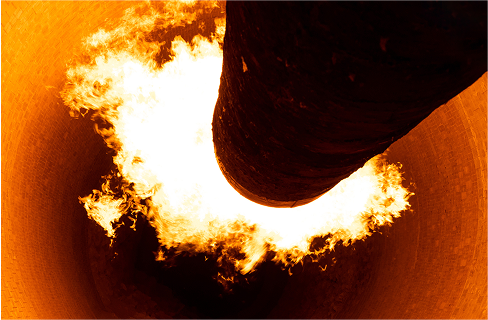
Current efficiency measures
Advanced manufacturing plants have already established energy-efficiency measures and the use of alternate fuels, while clinker substitution by waste or recycled materials is extensively practiced in the construction industry to reduce cement consumption. However, these measures are insufficient to achieve desired energy efficiency targets.
vs.
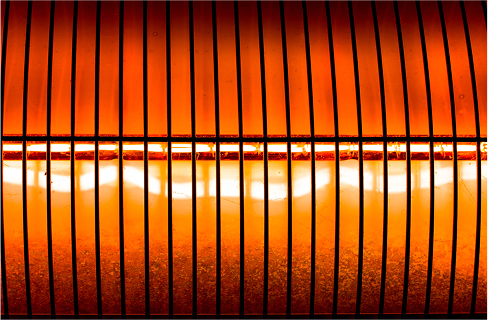
EPIXC’s electrification approach
Electrified and hybrid process heating of unit operations in cement manufacturing has started to receive attention. The challenge is to reach the high process temperatures required for cement manufacturing. The goal of EPIXC is to identify and develop electrified and hybrid heating alternatives for cement manufacturing, initially focusing on the calcination process. Electrically heated kilns could result in more uniform heat distribution, which would allow for a greater flexibility in feedstocks.
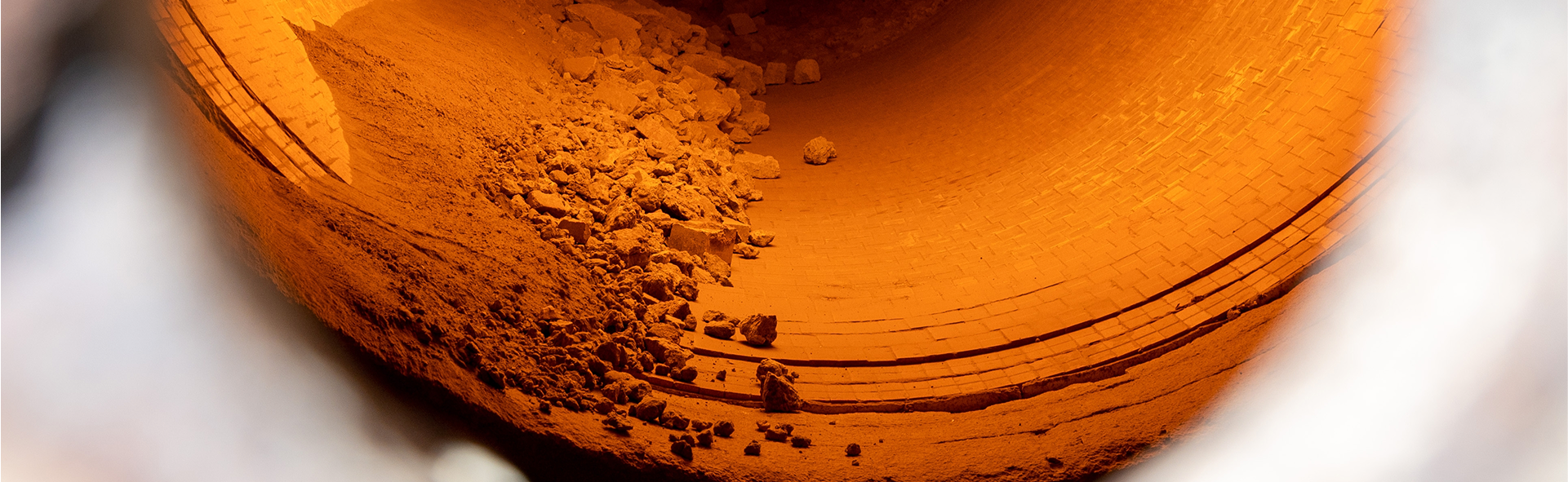
EPIXC’s impact on cement manufacturing
Through existing and emerging advanced electrified and hybrid process heating technologies, EPIXC is well positioned to advance the competitiveness of U.S. cement production, reduce manufacturing costs, improve product quality, enable broader heat process technology choices, and provide transparent, impartial systems-level analysis to inform technology readiness and adoption decisions. EPIXC works with established cement manufacturers as well as electrification and hybrid technology developers to drive energy efficiency and other benefits.
Join our mission
If you are interested in joining our mission, become a member today!